In addition to cell phone jammers, Faraday bags can also be widely used to protect electronic devices and personal privacy. The design and manufacture of Faraday bags seem simple, but in fact, several key issues need to be paid attention to to ensure their effectiveness and durability.
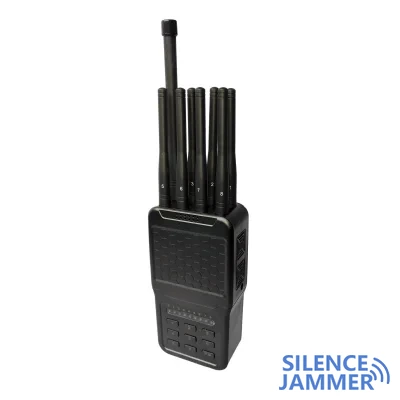
1. Material selection
The core of the Faraday bag lies in its material selection. The ideal material should have good conductivity and durability. Common materials include:
- Metal fiber fabric: This material can effectively shield electromagnetic waves in various frequency bands, such as copper fiber or nickel-copper coated fabric.
- Conductive film: Some high-end Faraday bags use conductive film, which is usually lighter and has good shielding effect.
- Composite materials: Some Faraday bags use composite materials, combining metal fibers with other materials to improve strength and durability.
In the material selection process, it is crucial to ensure that both its conductivity and mechanical properties meet the requirements.
2. Manufacturing process
The manufacturing process of Faraday bags directly affects their shielding effect and service life. The following aspects should be paid attention to during the manufacturing process:
- Suture technology: Suture is a key link in the production of Faraday bags. If the suture is not tight or the wire used is not conductive, electromagnetic signals may leak. Therefore, using conductive wire for suture and ensuring that each stitch fits tightly is the key to ensuring the shielding effect.
- Multi-layer design: In order to improve the shielding effect, many Faraday bags adopt a multi-layer design. Usually including an inner layer of conductive material and an outer layer of protective material. The multi-layer design not only enhances the shielding effect, but also increases the durability of the bag.
- Sealing design: The sealing part is where electromagnetic signals may leak. Using high-quality Velcro or zippers to ensure that the sealing is completely closed is the key to preventing signal leakage.
3. Shielding effect test
During the production process, testing the shielding effect of the Faraday bag is an essential step. Common test methods include:
- Electromagnetic compatibility (EMC) test: Use professional EMC test equipment to detect the shielding effect of the Faraday bag in different frequency bands. Ensure that it can effectively shield the signals of all target frequency bands.
- Field test: Put mobile phones, RFID cards and other electronic devices into the Faraday bag for actual use test to ensure that the signal is completely shielded.
Through rigorous testing, ensure that every Faraday bag has a good shielding effect when it leaves the factory.
4. Environmental protection and safety
In the manufacturing process of Faraday bags, environmental protection and safety issues also need to be paid attention to:
- Environmental protection of materials: Select environmentally friendly materials, avoid the use of harmful chemicals, and ensure the environmental performance of the product.
- Safety of the production process: During the production process, ensure the safety of workers, avoid contact with harmful substances, and provide necessary safety protection measures.
5. Product appearance and practicality
Although the main function of the Faraday bag is to shield electromagnetic signals, appearance and practicality are also the focus of consumers:
- Appearance design: Combined with market demand, design beautiful and fashionable appearance to attract consumers' attention. The diversity of colors, styles and sizes can meet the needs of different users.
- Convenience of use: During the design process, the user's convenience of use is taken into consideration. For example, adding hooks, zippers and other details that are easy to carry makes the Faraday bag not only powerful but also has a good user experience.
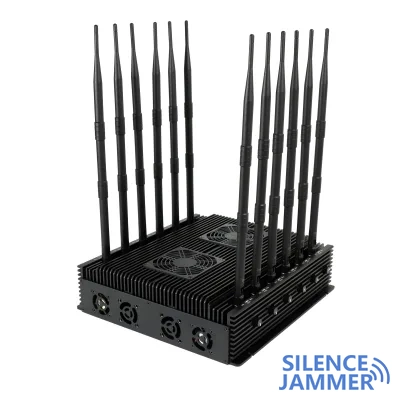
6. Quality Control
During the production process, a strict quality control system is established to ensure that every Faraday bag meets the standards:
- Raw material testing: All raw materials entering the production line are tested to ensure that their conductivity and mechanical properties meet the requirements.
- Production process monitoring: During the production process, every link is monitored to ensure that the process meets the standards.
- Finished product inspection: Each finished product is fully tested, including appearance, size, shielding effect, etc. to ensure product quality.
The manufacturing of Faraday bags involves multiple key links, from material selection, production process, shielding effect testing to environmental protection and safety issues, each link requires meticulous attention. Only when every detail is ensured to be in place can high-quality Faraday bags be produced to meet market demand.